Description
Our company provides SiC coating process services by CVD method on the surface of graphite, ceramics and other materials, so that special gases containing carbon and silicon react at high temperature to obtain high purity SiC molecules, molecules deposited on the surface of the coated materials, forming SIC protective layer.
The characteristics of SiC shower heads are as follows:
1. Corrosion resistance: SiC material has excellent corrosion resistance and can withstand the erosion of various chemical liquids and solutions, and is suitable for a variety of chemical processing and surface treatment processes.
2. High temperature stability: SiC nozzles can maintain structural stability in high temperature environments and are suitable for applications that require high temperature treatment.
3. Uniform spraying: SiC nozzle design has good spraying control performance, which can achieve uniform liquid distribution and ensure that the treatment liquid is evenly covered on the target surface.
4. High wear resistance: SiC material has high hardness and wear resistance and can withstand long-term use and friction.
SiC shower heads are widely used in liquid treatment processes in semiconductor manufacturing, chemical processing, surface coating, electroplating and other industrial fields. It can provide stable, uniform and reliable spraying effects to ensure the quality and consistency of processing and treatment.
Main Features
1. High temperature oxidation resistance:
the oxidation resistance is still very good when the temperature is as high as 1600 C.
2. High purity: made by chemical vapor deposition under high temperature chlorination condition.
3. Erosion resistance: high hardness, compact surface, fine particles.
4. Corrosion resistance: acid, alkali, salt and organic reagents.
Main Specifications of CVD-SIC Coating
SiC-CVD Properties | ||
Crystal Structure | FCC β phase | |
Density | g/cm ³ | 3.21 |
Hardness | Vickers hardness | 2500 |
Grain Size | μm | 2~10 |
Chemical Purity | % | 99.99995 |
Heat Capacity | J·kg-1 ·K-1 | 640 |
Sublimation Temperature | ℃ | 2700 |
Felexural Strength | MPa (RT 4-point) | 415 |
Young’ s Modulus | Gpa (4pt bend, 1300℃) | 430 |
Thermal Expansion (C.T.E) | 10-6K-1 | 4.5 |
Thermal conductivity | (W/mK) | 300 |
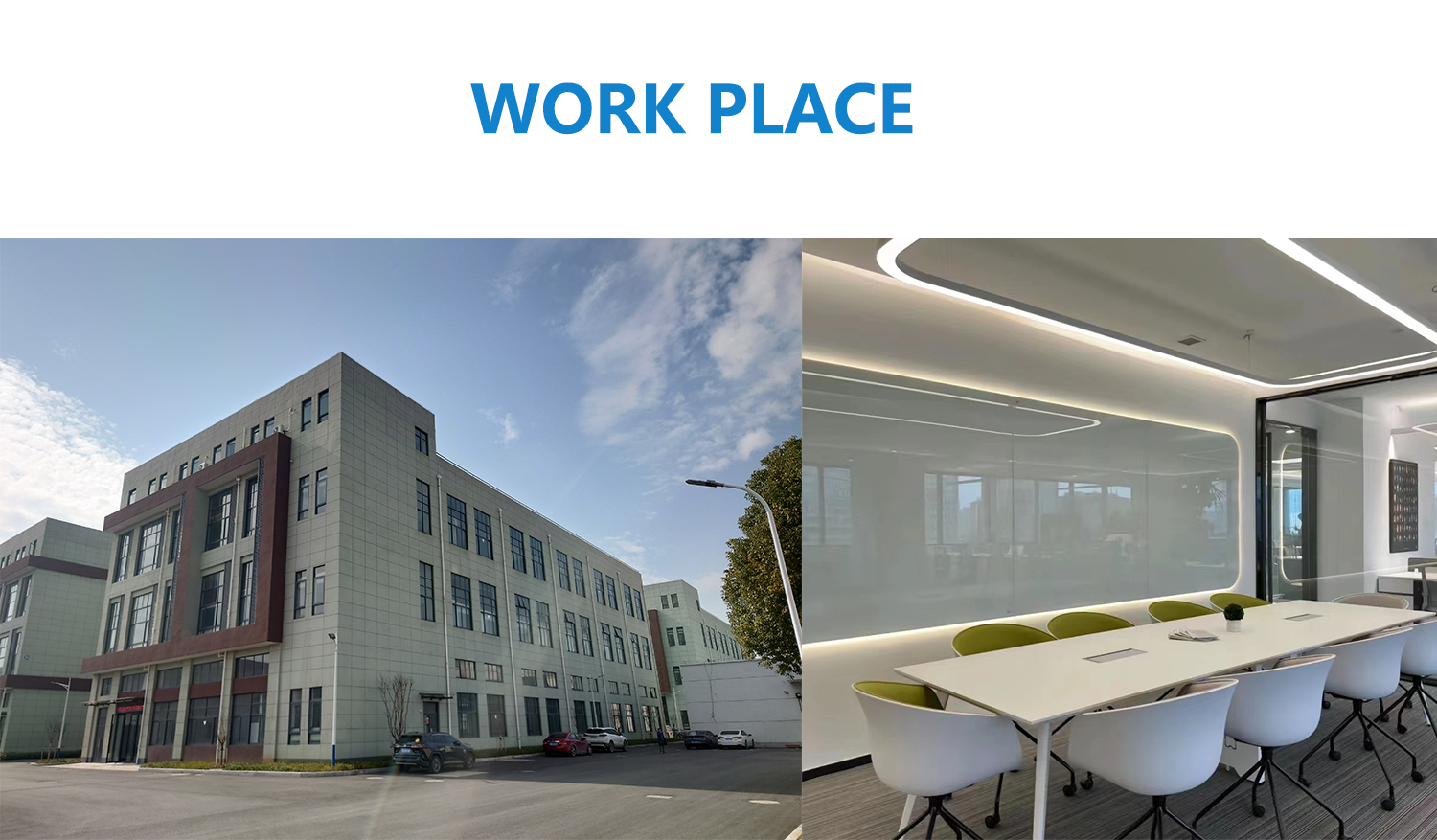
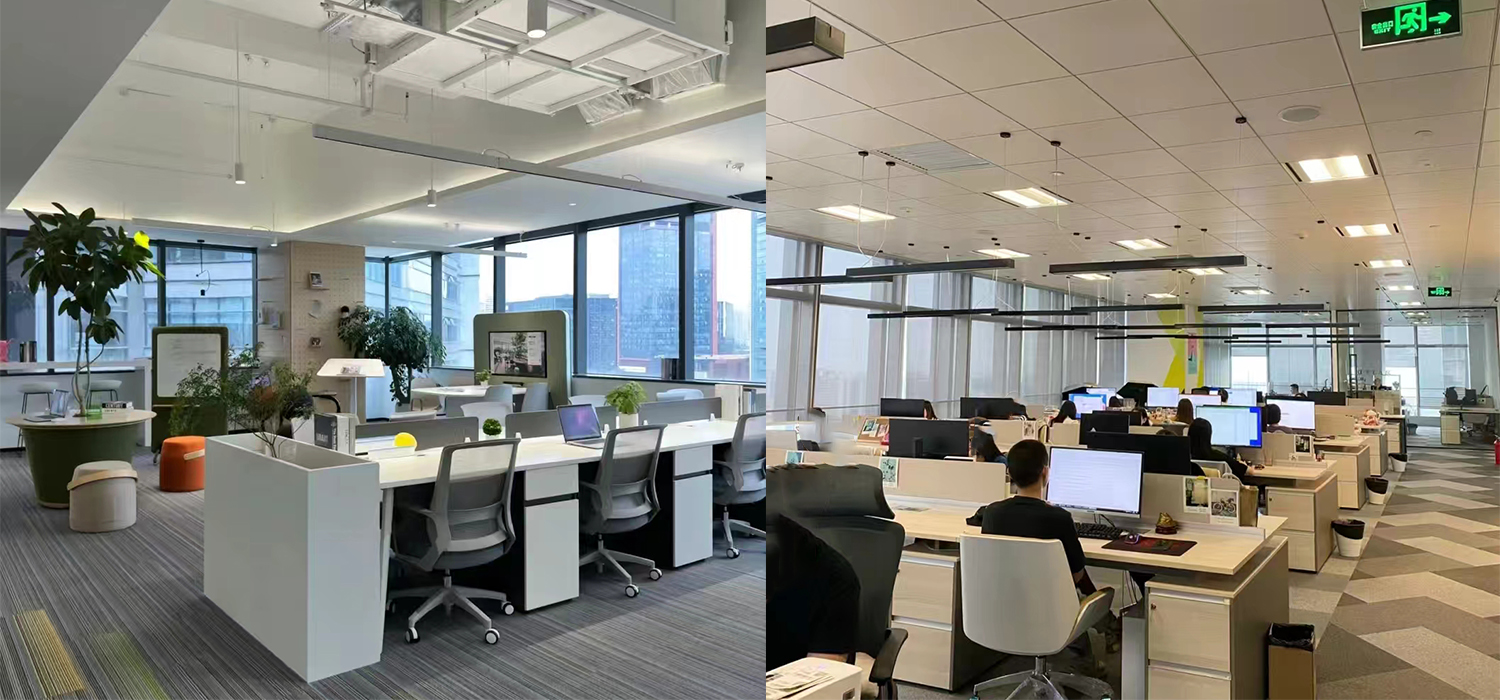
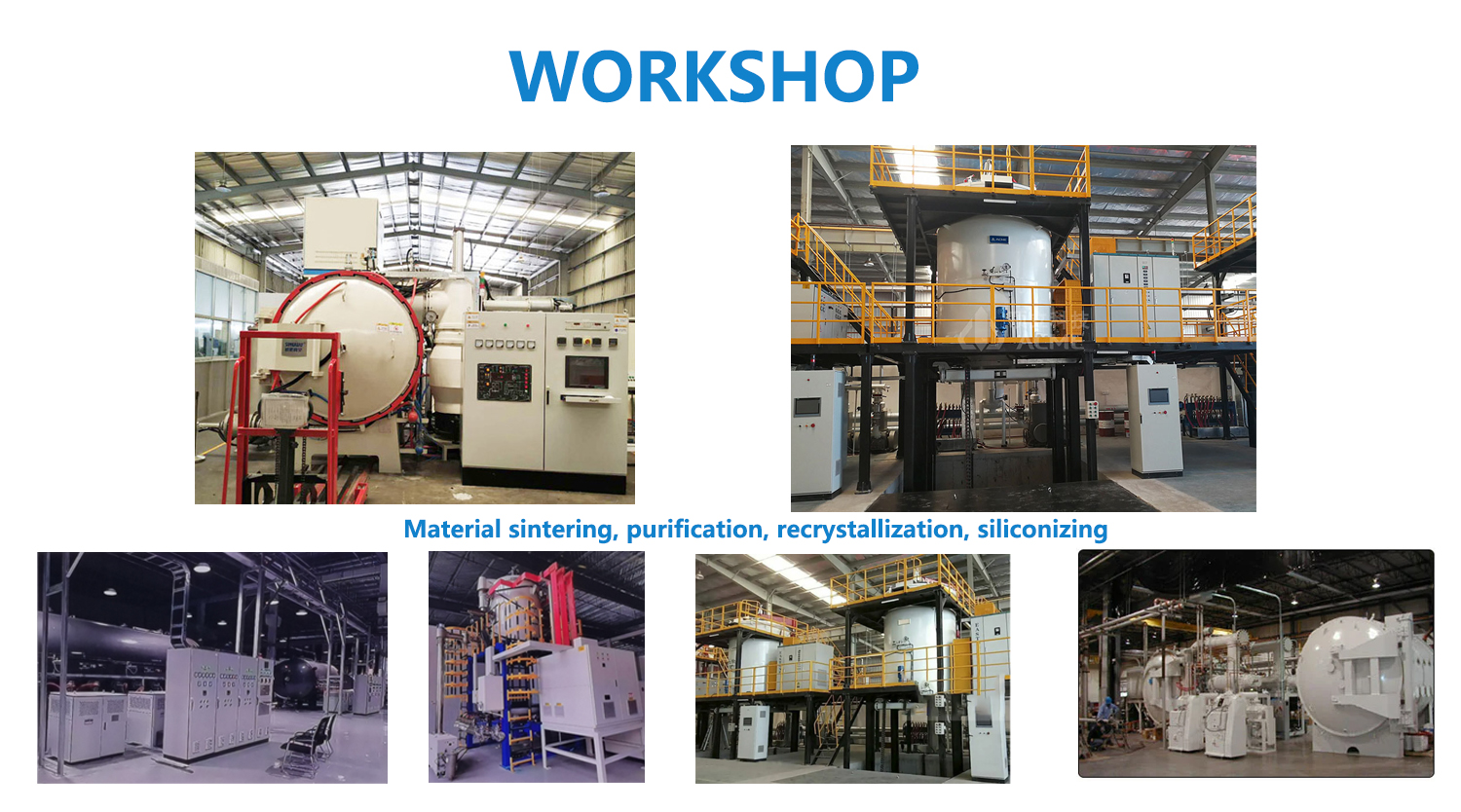
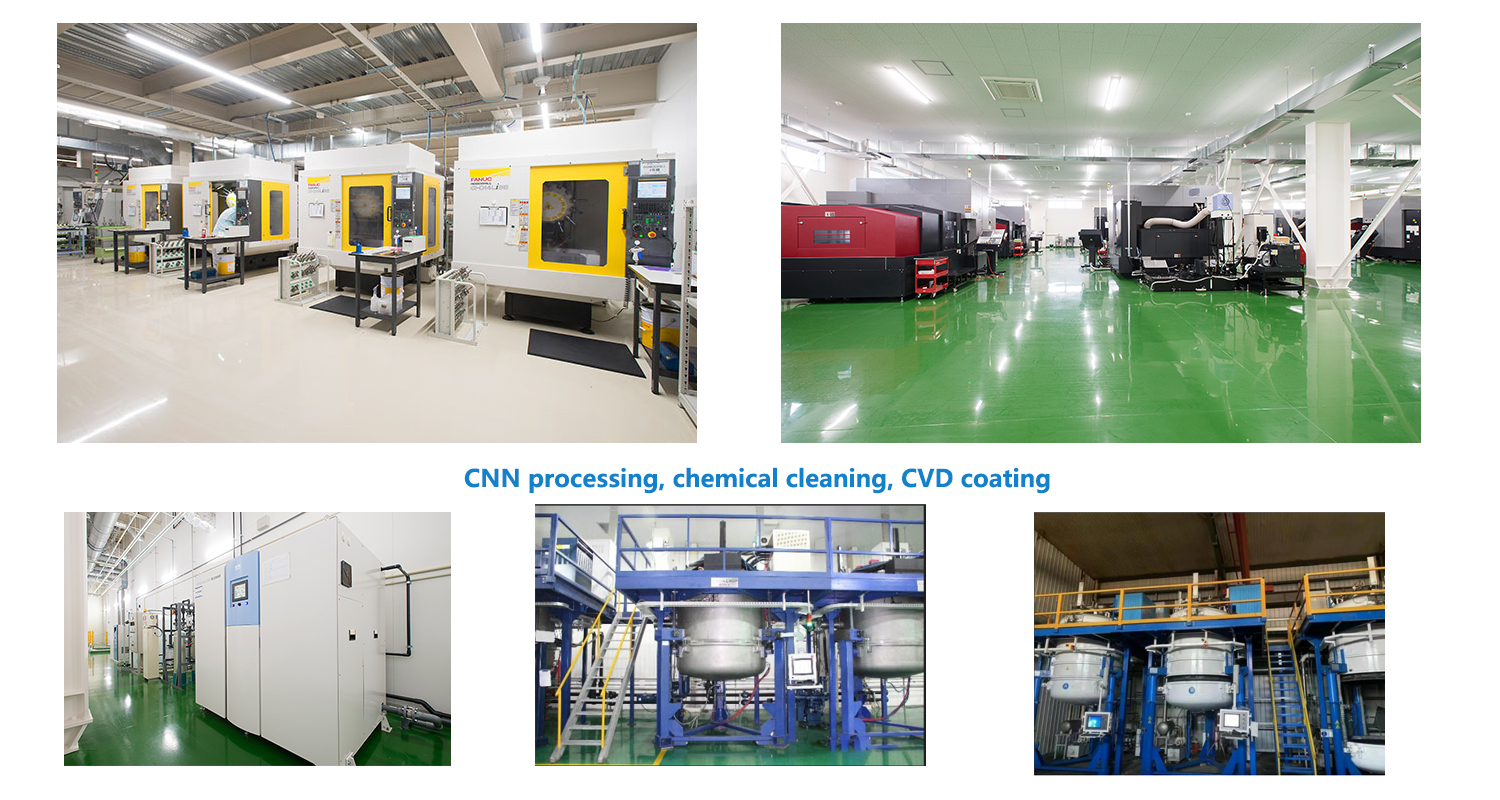
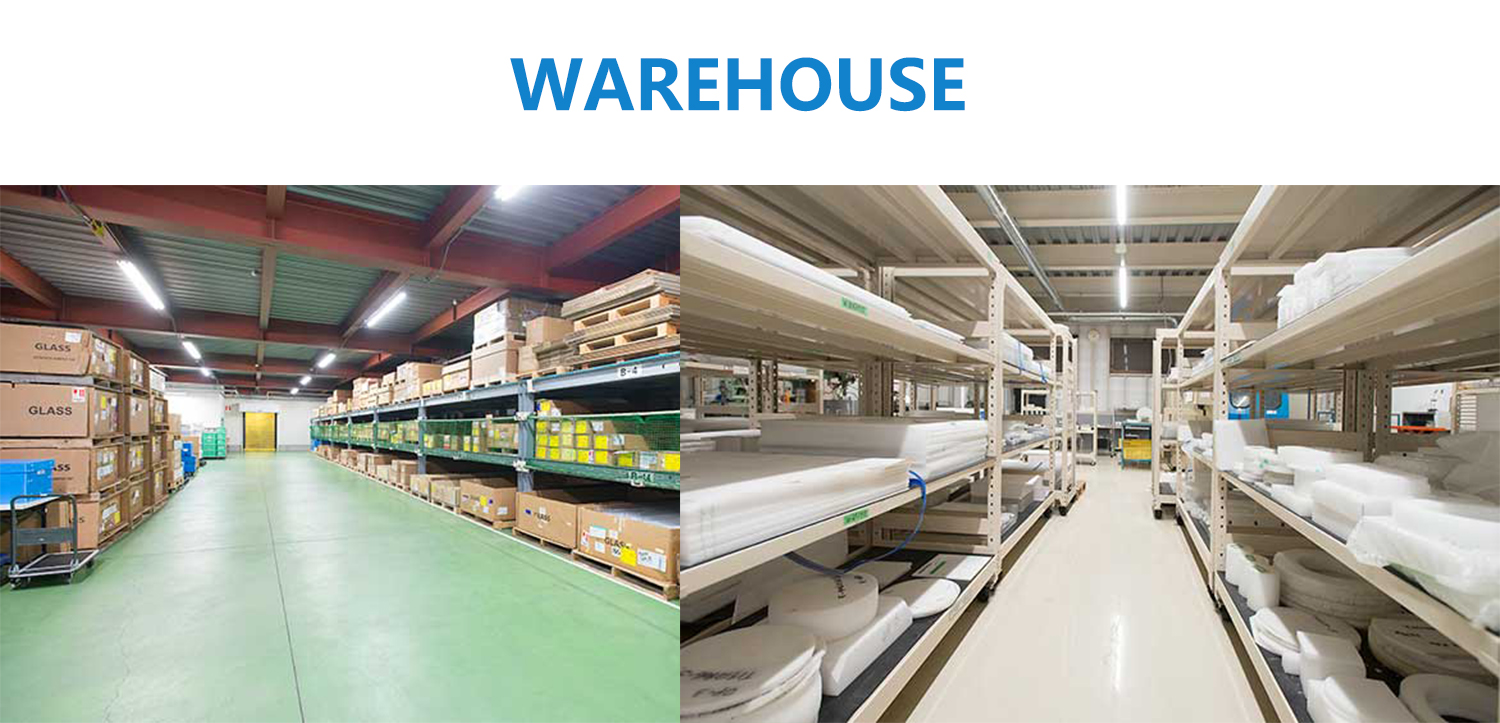
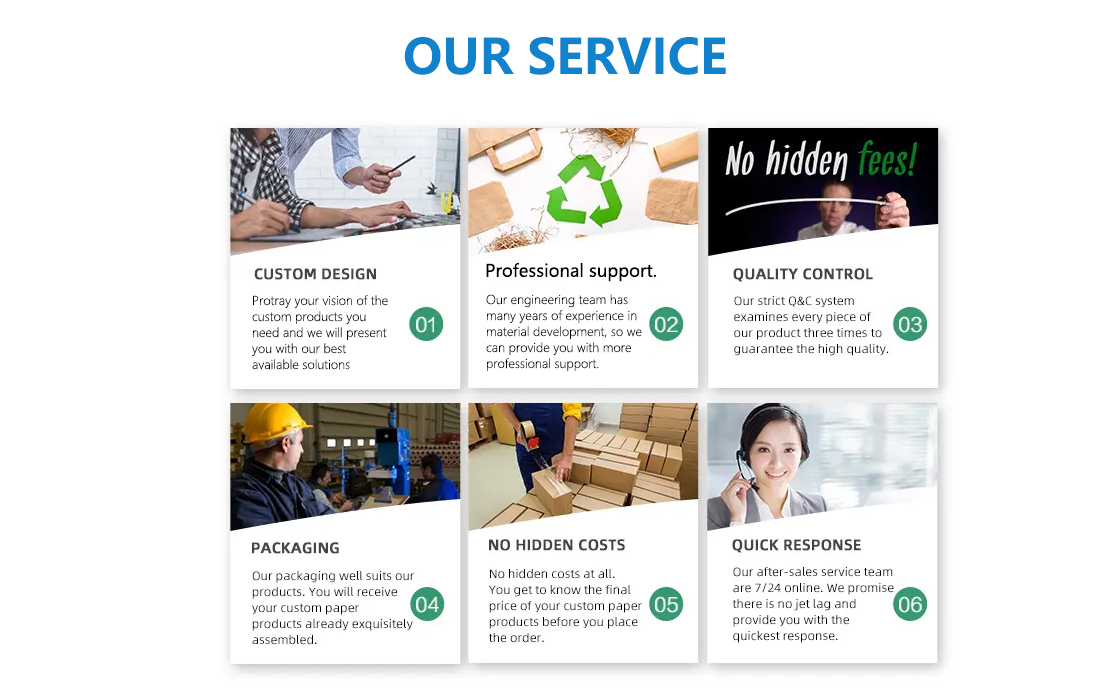