Silicon nitride (Si₃N₄) ceramics, as advanced structural ceramics, possess excellent properties such as high temperature resistance, high strength, high toughness, high hardness, creep resistance, oxidation resistance, and wear resistance. Additionally, they offer good thermal shock resistance, dielectric properties, high thermal conductivity, and excellent high-frequency electromagnetic wave transmission performance. These outstanding comprehensive properties make them widely used in complex structural components, especially in aerospace and other high-tech fields.
However, Si₃N₄, being a compound with strong covalent bonds, has a stable structure that makes sintering to high density difficult through solid-state diffusion alone. To promote sintering, sintering aids, such as metal oxides (MgO, CaO, Al₂O₃) and rare earth oxides (Yb₂O₃, Y₂O₃, Lu₂O₃, CeO₂), are added to facilitate densification via a liquid-phase sintering mechanism.
Currently, global semiconductor device technology is advancing toward higher voltages, larger currents, and greater power densities. Research into methods for fabricating Si₃N₄ ceramics is extensive. This article introduces sintering processes that effectively improve the density and comprehensive mechanical properties of silicon nitride ceramics.
Common Sintering Methods for Si₃N₄ Ceramics
Comparison of Performance for Si₃N₄ Ceramics Prepared by Different Sintering Methods
1. Reactive Sintering (RS): Reactive sintering was the first method used to industrially prepare Si₃N₄ ceramics. It is simple, cost-effective, and capable of forming complex shapes. However, it has a long production cycle, which is not conducive to industrial-scale production.
2. Pressureless Sintering (PLS): This is the most basic and simple sintering process. However, it requires high-quality Si₃N₄ raw materials and often results in ceramics with lower density, significant shrinkage, and a tendency to crack or deform.
3. Hot-Press Sintering (HP): The application of uniaxial mechanical pressure increases the driving force for sintering, allowing dense ceramics to be produced at temperatures 100-200°C lower than those used in pressureless sintering. This method is typically used for fabricating relatively simple block-shaped ceramics but is difficult to meet the thickness and shape requirements for substrate materials.
4. Spark Plasma Sintering (SPS): SPS is characterized by fast sintering, grain refinement, and reduced sintering temperatures. However, SPS requires significant investment in equipment, and the preparation of high thermal conductivity Si₃N₄ ceramics via SPS is still in the experimental stage and has not yet been industrialized.
5. Gas-Pressure Sintering (GPS): By applying gas pressure, this method inhibits ceramic decomposition and weight loss at high temperatures. It is easier to produce high-density ceramics and enables batch production. However, a single-step gas-pressure sintering process struggles to produce structural components with uniform internal and external color and structure. Using a two-step or multi-step sintering process can significantly reduce intergranular oxygen content, improve thermal conductivity, and enhance overall properties.
However, the high sintering temperature of two-step gas-pressure sintering has led previous research to focus mainly on preparing Si₃N₄ ceramic substrates with high thermal conductivity and room-temperature bending strength. Research on Si₃N₄ ceramics with comprehensive mechanical properties and high-temperature mechanical properties is relatively limited.
Gas-Pressure Two-Step Sintering Method for Si₃N₄
Yang Zhou and colleagues from Chongqing University of Technology used a sintering aid system of 5 wt.% Yb₂O₃ + 5 wt.% Al₂O₃ to prepare Si₃N₄ ceramics using both one-step and two-step gas-pressure sintering processes at 1800°C. The Si₃N₄ ceramics produced by the two-step sintering process had higher density and better comprehensive mechanical properties. The following summarizes the effects of one-step and two-step gas-pressure sintering processes on the microstructure and mechanical properties of Si₃N₄ ceramic components.
Density The densification process of Si₃N₄ typically involves three stages, with overlap between the stages. The first stage, particle rearrangement, and the second stage, dissolution-precipitation, are the most critical stages for densification. Sufficient reaction time in these stages significantly improves sample density. When the pre-sintering temperature for the two-step sintering process is set to 1600°C, β-Si₃N₄ grains form a framework and create closed pores. After pre-sintering, further heating under high temperature and nitrogen pressure promotes liquid-phase flow and filling, which helps eliminate closed pores, further improving the density of Si₃N₄ ceramics. Therefore, the samples produced by the two-step sintering process show higher density and relative density than those produced by one-step sintering.
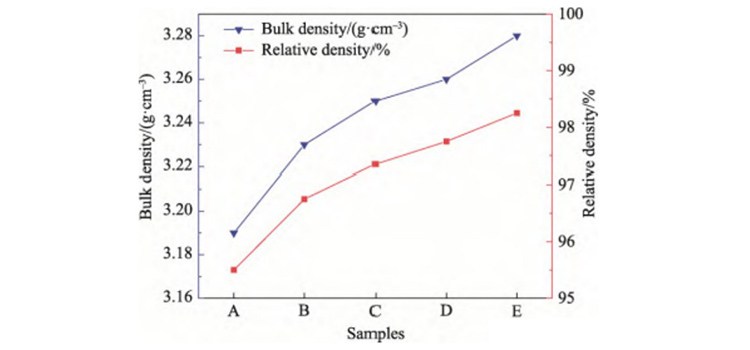
Phase and Microstructure During one-step sintering, the time available for particle rearrangement and grain boundary diffusion is limited. In the two-step sintering process, the first step is conducted at low temperature and low gas pressure, which extends the particle rearrangement time and results in larger grains. The temperature is then increased to the high-temperature stage, where the grains continue to grow through the Ostwald ripening process, yielding high-density Si₃N₄ ceramics.
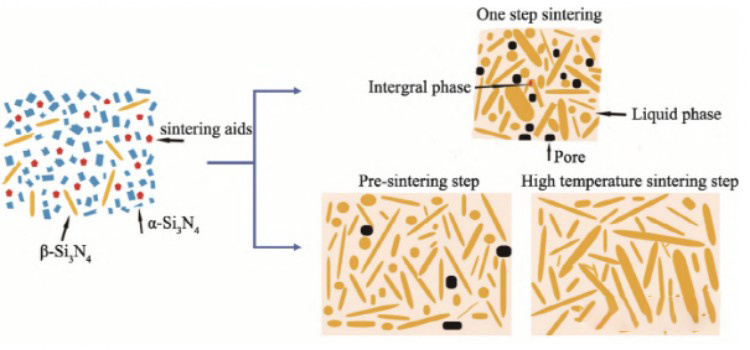
Mechanical Properties The softening of the intergranular phase at high temperatures is the primary reason for reduced strength. In one-step sintering, abnormal grain growth creates small pores between the grains, which prevents significant improvement in high-temperature strength. However, in the two-step sintering process, the glass phase, uniformly distributed in the grain boundaries, and the uniformly sized grains enhance the intergranular strength, resulting in higher high-temperature bending strength.
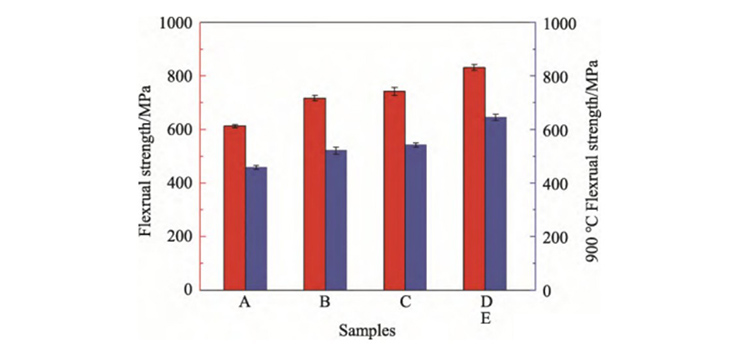
In conclusion, prolonged holding during one-step sintering can effectively reduce internal porosity and achieve uniform internal color and structure but may lead to abnormal grain growth, which degrades certain mechanical properties. By employing a two-step sintering process—using low-temperature pre-sintering to extend particle rearrangement time and high-temperature holding to promote uniform grain growth—a Si₃N₄ ceramic with relative density of 98.25%, uniform microstructure, and excellent comprehensive mechanical properties can be successfully prepared.
Name | Substrate | Epitaxial layer composition | Epitaxial process | Epitaxial medium |
Silicon homoepitaxial | Si | Si | Vapor Phase Epitaxy (VPE) |
SiCl4+H2 |
Silicon heteroepitaxial | Sapphire or spinel | Si | Vapor Phase Epitaxy (VPE) | SiH₄+H₂ |
GaAs homoepitaxial |
GaAs |
GaAs GaAs |
Vapor Phase Epitaxy (VPE) |
AsCl₃+Ga+H₂ (Ar) |
GaAs |
GaAs GaAs |
Molecular Beam Epitaxy (MBE) |
Ga+As |
|
GaAs heteroepitaxial | GaAs GaAs |
GaAlAs/GaAs/GaAlAs |
Liquid Phase Epitaxy (LPE)
Vapor Phase (VPE) |
Ga+Al+CaAs+ H2
Ga+AsH3+PH3+CHl+H2 |
GaP homoepitaxial |
GaP |
GaP(GaP;N) |
Liquid Phase Epitaxy (LPE)
Liquid Phase Epitaxy (LPE) |
Ga+GaP+H2+(NH3)
Ga+GaAs+GaP+NH3 |
Superlattice | GaAs | GaAlAs/GaAs (cycle) |
Molecular Beam Epitaxy (MBE)
MOCVD |
Ca,As,Al
GaR₃+AlR3+AsH3+H2 |
InP homoepitaxial |
InP |
InP |
Vapor Phase Epitaxy (VPE)
Liquid Phase Epitaxy (LPE) |
PCl3+In+H2
In+InAs+GaAs+InP+H₂ |
Si/GaAs Epitaxy |
Si |
GaAs |
Molecular Beam Epitaxy (MBE)
MOGVD |
Ga、As
GaR₃+AsH₃+H₂ |
Post time: Dec-24-2024