Silicon carbide(SiC) epitaxy
The epitaxial tray, which holds the SiC substrate for growing the SiC epitaxial slice, placed in the reaction chamber and directly contacts the wafer.


The upper half-moon part is a carrier for other accessories of the reaction chamber of Sic epitaxy equipment,while the lower half-moon part is connected to the quartz tube, introducing the gas to drive the susceptor base to rotate. they are temperature-controllable and installed in the reaction chamber without direct contact with the wafer.
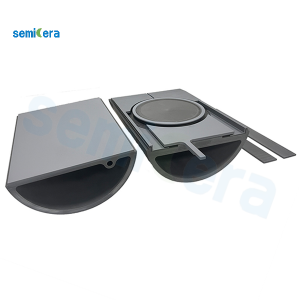
Si epitaxy
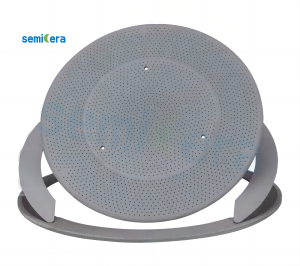
The tray, which holds the Si substrate for growing the Si epitaxial slice, placed in the reaction chamber and directly contacts the wafer.

The preheating ring is located on the outer ring of the Si epitaxial substrate tray and is used for calibration and heating. It is placed in the reaction chamber and does not directly contact the wafer.

An epitaxial susceptor, which holds the Si substrate for growing an Si epitaxial slice, placed in the reaction chamber and directly contacts the wafer.

Epitaxial barrel is key components used in various semiconductor manufacturing processes, generally used in MOCVD equipment, with excellent thermal stability, chemical resistance and wear resistance, very suitable for use in high temperature processes. It contacts the wafers.

Physical properties of Recrystallized Silicon Carbide |
|
Property | Typical Value |
Working temperature (°C) | 1600°C (with oxygen), 1700°C (reducing environment) |
SiC content | > 99.96% |
Free Si content | <0.1% |
Bulk density | 2.60-2.70 g/cm 3 |
Apparent porosity | < 16% |
Compression strength | > 600 MPa |
Cold bending strength | 80-90 MPa (20°C) |
Hot bending strength | 90-100 MPa (1400°C) |
Thermal expansion @1500°C | 4.70 10 -6 /°C |
Thermal conductivity @1200°C | 23 W/m•K |
Elastic modulus | 240 GPa |
Thermal shock resistance | Extremely good |
Physical properties of Sintered Silicon Carbide |
|
Property | Typical Value |
Chemical Composition | SiC>95%, Si<5% |
Bulk Density | >3.07 g/cm³ |
Apparent porosity | <0.1% |
Modulus of rupture at 20℃ | 270 MPa |
Modulus of rupture at 1200℃ | 290 MPa |
Hardness at 20℃ | 2400 Kg/mm² |
Fracture toughness at 20% | 3.3 MPa · m1/2 |
Thermal Conductivity at 1200℃ | 45 w/m .K |
Thermal expansion at 20-1200℃ | 4.5 1 ×10 -6 /℃ |
Max.working temperature | 1400℃ |
Thermal shock resistance at 1200℃ | Good |
Basic physical properties of CVD SiC films |
|
Property | Typical Value |
Crystal Structure | FCC β phase polycrystalline, mainly (111) oriented |
Density | 3.21 g/cm³ |
Hardness 2500 | (500g load) |
Grain Size | 2~10μm |
Chemical Purity | 99.99995% |
Heat Capacity | 640 J·kg -1 ·K -1 |
Sublimation Temperature | 2700℃ |
Flexural Strength | 415 MPa RT 4-point |
Young's Modulus | 430 Gpa 4pt bend, 1300℃ |
Thermal Conductivity | 300W·m-1 ·K -1 |
Thermal Expansion(CTE) | 4.5×10 -6 K -1 |
Main features
The surface is dense and free of pores.
High purity, total impurity content <20ppm, good airtightness.
High temperature resistance, strength increases with increasing usage temperature, reaching the highest value at 2750℃,sublimation at 3600℃.
Low elastic modulus, high thermal conductivity, low thermal expansion coefficient, and excellent thermal shock resistance.
Good chemical stability, resistant to acid, alkali, salt, and organic reagents, and has no effect on molten metals, slag, and other corrosive media. It does not oxidize significantly in the atmosphere below 400 C, and the oxidation rate significantly increases at 800 ℃.
Without releasing any gas at high temperatures, it can maintain a vacuum of10-7mmHg at around 1800°C.
Product application
Melting crucible for evaporation in semiconductor industry.
High power electronic tube gate.
Brush that contacts the voltage regulator.
Graphite monochromator for X-ray and neutron.
Various shapes of graphite substrates and atomic absorption tube coating.
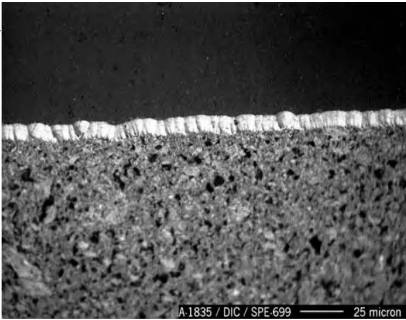
Pyrolytic carbon coating effect under a 500X microscope, with intact and sealed surface.
TaC coating is the new generation high temperature resistant material, with better high temperature stability than SiC. As a corrosion-resistant coating, anti-oxidation coating and wear-resistant coating, can be used in the environment above 2000C, widely used in aerospace ultra-high temperature hot end parts, the third generation semiconductor single crystal growth fields.
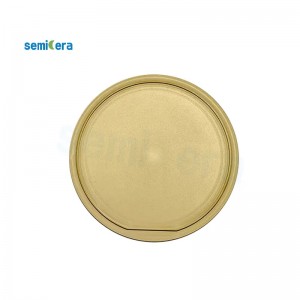
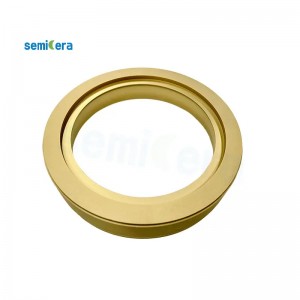
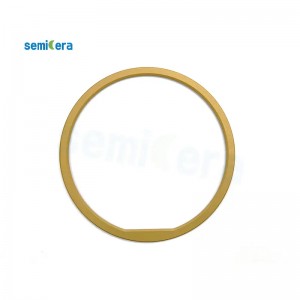
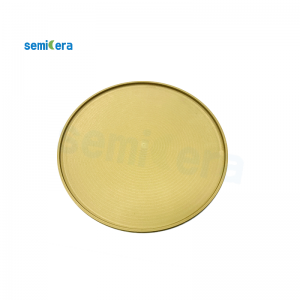
Physical properties of TaC coating | |
Density | 14.3 (g/cm3) |
Specific emissivity | 0.3 |
Thermal expansion coefficient | 6.3 10/K |
Hardness (HK) | 2000 HK |
Resistance | 1x10-5 Ohm*cm |
Thermal stability | <2500℃ |
Graphite size changes | -10~-20um |
Coating thickness | ≥220um typical value (35um±10um) |
Solid CVD SILICON CARBIDE parts are recognized as the primary choice for RTP/EPI rings and bases and plasma etch cavity parts that operate at high system required operating temperatures (> 1500°C), the requirements for purity are particularly high (> 99.9995%) and the performance is especially good when the resistance tol chemicals is particularly high. These materials do not contain secondary phases at the grain edge, so theil components produce fewer particles than other materials. In addition, these components can be cleaned usingl hot HF/HCI with little degradation, resulting in fewer particles and a longer service life.
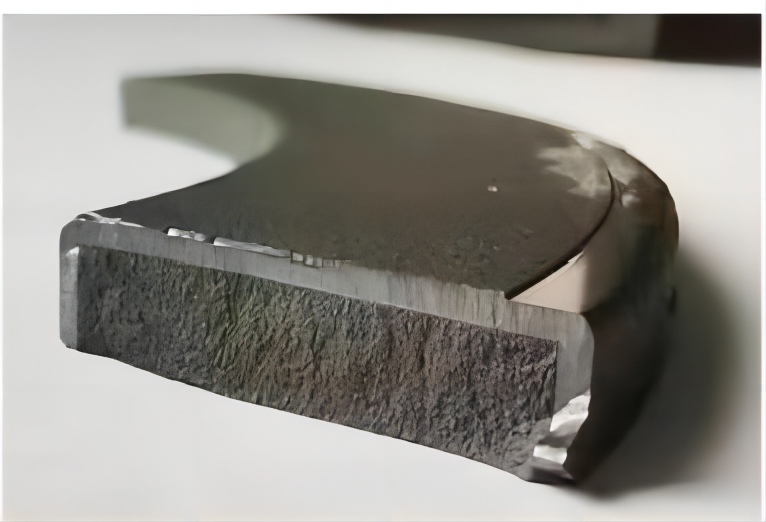
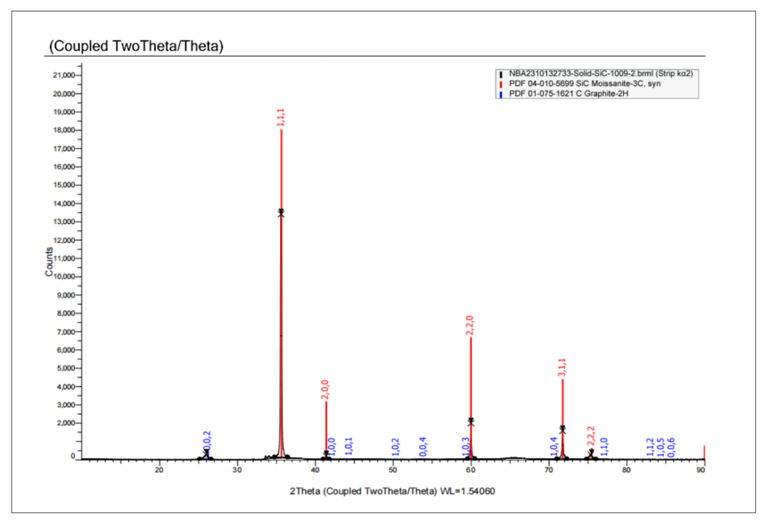